Downloads
Download


This work is licensed under a Creative Commons Attribution 4.0 International License.
Article
Study on Combustion and Soot Formation Characteristics of RCCI Engine with Diesel Mixed with PODE Ignited Gasoline
Qian Wang, Botian Guo, Wenjun Zhong *, Peng Jiang *, and Xu Liu
School of Energy and Power Engineering, Jiangsu University, Zhenjiang 212013, China
* Correspondence: wj_zhong@ujs.edu.cn (W.Z.); jiangpeng@ujs.edu.cn (P.J.)
Received: 8 November 2023
Accepted: 23 January 2024
Published: 30 January 2024
Abstract: Polymethoxydimethyl ether (PODE) is a promising clean alternative fuel with the potential to improve carbon emissions from internal combustion engines. However, when used as a sole fuel, its low viscosity leads to increased wear on high-pressure pumps and injectors. Furthermore, its low calorific value makes it unsuitable for direct application in diesel engines. Numerous studies have shown that blending PODE with diesel results in lower soot generation throughout the entire combustion cycle in diesel engines. However, the process of reducing in-cylinder soot generation is not yet clear, necessitating further optical diagnostics of in-cylinder combustion. Therefore, the aim of this study is to investigate the influence of PODE/diesel blend combustion on the combustion characteristics and soot generation properties of reactivity controlled compression ignition (RCCI) diesel engines. The study employs an optical engine and conducts experiments using high-speed imaging and two-color pyrometry. Preliminary experiments indicate that a 50% premixed ratio exhibits better heat release and lower soot generation. Thus, this study explores the effects on in-cylinder combustion and soot generation properties by varying the PODE blending ratio and injection strategy under a 50% premixed ratio. Results indicate that with an increase in PODE blending ratio, both peak in-cylinder pressure and heat release rate decrease, and the combustion duration is prolonged. Compared to diesel, the soot content of P20D80 (20% PODE and 80% diesel) and P50D50 (50% PODE and 50% diesel) is 55.22% and 36.55% respectively, while the heat release is 97.89% and 95.39% of that of diesel. The total amount of soot generated was 55.22% and 36.55% of that of direct injection P0D100, the high temperature area of soot was reduced by 52.9% and 73.32% respectively, the stable value of the average soot temperature was reduced by 6.65 K and 20.25 K respectively, and the average KL factor was the stability values were reduced by 10.35% and 16.12% respectively. P50D50 effectively reduces soot generation while maintaining thermal efficiency. Furthermore, an investigation of injection strategy under P50D50 condition reveals that segmented injection results in lower cylinder pressure, peak heat release rate, and total soot generation compared to single injection. The average temperature of the two-stage injection strategy increased, and the average temperature of soot stable time under the operating conditions of D-40/-20, D-35/-20 and D-30/-20 were 2100.85 K, 2210.16 K and 2192.24 K, respectively. The stable values of the average KL factor of soot under the operating conditions of D-40/-20, D-35/-20 and D-30/-20 were 86.52%, 66.62% and 62.79% of those of S-20, respectively. Although it effectively suppresses soot generation, it comes at the cost of sacrificing a portion of heat release.
Keywords:
polymethoxydimethyl ether (PODE) optical engine two-color method soot temperature KL injection strategy1. Introduction
In the context of escalating global greenhouse gas concerns, urgent measures are imperative to conserve energy and mitigate emissions within the combustion engine sector. The pursuit of carbon peaking and neutrality has instigated fresh imperatives for the curtailment of carbon emissions arising from combustion engines [1]. Concurrently, enhancing the thermal efficiency of internal combustion engines while effecting emissions reduction has emerged as a pivotal trajectory in their development. Notably, the heightened levels of nitrogen oxides (NOX) and soot emissions characteristic of conventional diesel combustion (CDC) have rendered this mode of combustion challenging in meeting pertinent emission standards. In addition to dependence on post-treatment systems for emissions mitigation, there has been a surge of interest in recent years in exploring alternative combustion modes as a means to alleviate emissions.
In addressing NOX and soot emissions, prior studies have underscored the superior cleanliness of Low-Temperature Combustion (LTC) in comparison to conventional diesel engine combustion [2]. Among the LTC concepts, Homogeneous Charge Compression Ignition (HCCI) stands as an earlier proposition [3]. Extensive research conducted by numerous scholars has demonstrated that through the utilization of elevated levels of exhaust gas recirculation (EGR) and advanced injection timing, NOX and soot emissions can be nearly eliminated [4]. Furthermore, HCCI exhibits superior combustion thermal efficiency when compared to Conventional Diesel Combustion (CDC) due to the complete combustion of a homogeneous fuel-air mixture.
Nonetheless, the practicable operational range of HCCI is severely constrained as engine load increases [5]. This limitation arises from the escalating combustion pressure and temperature associated with load increment. Governed by chemical kinetics, combustion initiates at earlier stages of the compression stroke, leading to heightened pressure rise rates and excessive combustion noise. Additionally, HCCI’s low-temperature combustion leads to elevated emissions of carbon monoxide (CO) and unburned hydrocarbons (UHC) [6]. Consequently, HCCI encounters challenges in achieving broad-scale implementation in real-world engines. To tackle this issue, scholars have proposed the concept of Partially Premixed Combustion (PPC). In comparison to HCCI, PPC employs delayed injection timing to enhance the stratification of the in-cylinder fuel-air mixture, thereby refining combustion control [7]. Nevertheless, the high cetane number of diesel and similar fuels constrains the potential for PPC to extend its operational range under high loads.
Professor Reitz of the University of Wisconsin introduced the concept of Reactivity Controlled Compression Ignition (RCCI) [8], which has garnered extensive attention and global scholarly interest. RCCI stands out from other combustion modes due to its capacity to regulate the combustion phase through the manipulation of fuel proportions. This adaptability considerably expands the operational scope of RCCI in comparison to alternative modes, resulting in minimal instances of knocking and detonation [9]. In a study by Kokjohn et al. [10], RCCI engines were compared with conventional diesel engines, revealing that RCCI combustion can achieve nearly negligible emissions of nitrogen oxides (NOX) and soot. Simulation results further demonstrated RCCI’s proficiency in governing the onset and culmination of in-cylinder combustion, consequently reducing heat transfer losses during combustion and markedly enhancing fuel conversion efficiency.
These research findings unequivocally establish that the Reactivity Controlled Compression Ignition (RCCI) concept attains higher indicated thermal efficiency and ultra-low emissions compared to conventional diesel engine combustion (CDC). As previously mentioned, the RCCI concept was initially explored using traditional fossil fuels like gasoline and diesel. However, some researchers have shifted their focus towards the utilization of renewable fuels as a pivotal strategy to alleviate the energy crisis and foster sustainable development. Among them, Wang et al. [11]. studied diesel / methanol dual fuel combustion. The results show that the oxidation activity of soot increases and the soot particle size decreases with the increase of methanol ratio. Zheng et al. [12]. studied biodiesel / n-butanol dual fuel combustion and showed lower soot, HC, CO emissions and slightly higher NOx. In addition, Jin et al. [13,14]. tested the solubility of diesel oil and alcohol, the results show that the solubility increases gradually with the increase of temperature, and the diesel microemulsion prepared by isopropanol / n-butanol / ethanol (IBE) has a good application prospect as a new composite fuel in diesel engine. NadirYilmaz et al. [15,16]. have proved that higher alcohols can be used as the third component of biodiesel-diesel mixture to improve fuel performance and reduce emissions. In addition, in another study, it was found that cetane number improver significantly reduced brake specific fuel consumption (BSFC) and nitrogen oxides (NOx) and increased carbon monoxide (CO) emissions, but had the opposite effect on hydrocarbon (HC) emissions.
The above studies show that alternative fuels can significantly improve the combustion performance and emissions. In addition to alcohol fuels, PODE attracts people’s attention among many alternative fuels. Due to its unique physical and chemical properties, including the absence of Cmurc C bond, increased cetane number and high oxygen content, soot emissions are effectively reduced. [17]. As a coal-based and biomass-derived oxygenated fuel, PODE is recognized as a promising substitute for petroleum-based fuels, attributed to its favorable physicochemical attributes and outstanding combustion and emission characteristics in engines. This has prompted numerous experimental studies investigating the application of PODE in diesel engines.
Wang et al. [18]. conducted combustion tests on PODE in a single-cylinder engine, revealing a significant response at low temperatures and an effective reduction in in-cylinder flame temperature. Iannuzzi et al. [19]. conducted a blending test using PODE in a heavy-duty diesel engine and observed a significant improvement in soot emissions with a 10% PODE blend. Duraisamy G et al. [20]. investigated and compared the combustion effects of diesel/methanol and PODE/methanol Reactivity Controlled Compression Ignition (RCCI) in a three-cylinder turbocharged CRDI diesel engine. The results indicated that an increased methanol mass fraction extended ignition delay time and reduced cylinder combustion pressure for both fuel combinations. This led to decreased nitrogen oxides and soot emissions from in-cylinder combustion. Notably, PODE/methanol RCCI combustion exhibited superior cleanliness compared to diesel/methanol RCCI combustion, with lower emissions of HC, CO, and soot. Tong et al. [21]. examined the combustion and emission characteristics of the PODE/Gasoline RCCI model and systematically assessed its potential for high-load expansion. The findings demonstrated that the PODE/Gasoline RCCI model achieved improvements in indicated thermal efficiency (ITE) and ultra-low smoke emissions compared to the Diesel/Gasoline RCCI model. The combustion stage had a more pronounced effect on PODE injection timing compared to the premix ratio. Advancing PODE injection timing shifted the combustion process from injection time control to overall reactivity control, influencing both premixing and diffusion combustion. Additionally, employing a single injection strategy extended the load range of the PODE/Gasoline RCCI mode to 1.76 MPa (IMEP) without excessive soot generation. Barro et al. [22]. investigated the combustion and emission characteristics of a blend consisting of 80% PODE3 and 20% PODE4 in a heavy-duty single-cylinder engine. The results indicated that PODE exhibited a shorter ignition delay period than diesel due to its high cetane number. This led to a reduced proportion of premix combustion and accelerated diffusion combustion. Consequently, without accounting for gas exchange cycles, the thermal efficiency of PODE surpassed that of diesel [23]. Ma et al. [24] found that when the PODE blending ratio was 20% and 50%, the total soot mass reduced by over 50% and over 95% respectively. Pellegrini et al. [25]. analyzed the emission characteristics of PODE in the engine and observed a substantial reduction in particulate matter (PM) emissions upon adding 10% PODE to diesel. However, CO2 and NOX emissions increased, while CO and HC emissions decreased. In addition, Shi et al. [26,27]. used low-temperature plasma injection system to regenerate diesel particulate filter (DPF) at low temperature (100°C). The results show that with the progress of DPF regeneration, O atoms are continuously bonded to PM to form oxidation intermediates containing Cmuro, Coluo and other functional groups, which improves the oxidation activity of PM. Under the condition of constant temperature, the higher the temperature, the lower the decomposition of PM.
The mentioned studies by these researchers have provided crucial insights into the combustion, blending, and emission behavior of PODE. Given PODE’s favorable combustion attributes and its capability to yield clean emissions, utilizing it as a high-reactivity fuel presents a potential solution to challenges encountered by gasoline-fueled Reactivity Controlled Compression Ignition (RCCI) engines. These challenges include difficulties in ignition at low load and high pre-mix ratio conditions, as well as issues pertaining to pollutant emissions at high load conditions.
Although a large number of engine bench experiments have explored the use of PODE as a highly reactive fuel in RCCI combustion there is a significant gap in the visual research on PODE ignition and flame development in RCCI engines. Therefore, in order to better understand the evolution process of flame and quantitatively evaluate the formation of soot, this study blends PODE in the pilot fuel (diesel) and adopts a flexible fuel injection strategy (two-stage injection strategy) to effectively reduce soot formation on the premise of efficient combustion. The flame characteristics and soot distribution are examined by high-speed imaging technology combined with two-color method, and the in-cylinder pressure curve, heat release rate curve, ignition delay period, duration, combustion phase, soot temperature distribution and soot KL factor distribution are analyzed to provide guidance for energy saving and carbon reduction in the future.
2. Methodology
2.1. Optical Engine Facility
In this study, a 4-cylinder, four-valve R425DOHC naturally aspirated diesel engine was used, and the third cylinder was modified to be an optical engine with a transparent window. The main parameters of the optical engine are shown in Table 1 and a schematic diagram of the main body of the engine is shown in Figure 1. To simulate real engine conditions, the engine was preheated by circulating water and started by an electric dynamometer with reverse towing. The dynamometer used in the experiment allowed speed adjustments in the range of 0 to 2000 revolutions per minute (r/min), with a specific test speed of 1200 r/min. Intake air was supplied by natural aspiration, and additional components such as a heater and pressure stabilizer were incorporated into the intake tract for improved control and stability.
Table 1. Test equipment of optical engine.
Figure 1. Schematic of optical engine test.
The test used Photron’s FASTCAMSA-Z high-speed camera model with a maximum recording speed of 224,000 fps. In this paper, the camera was set to shoot at 25,000 fps with 768 × 696 original pixels and 400 single-cycle images triggered by the moment of oil injection. Two filters with wavelengths of 550 nm and 660 nm were placed in front of the lens to observe the formation and evolution of the soot. To capture the luminescent signal of the flame, a high-speed camera was used, with an extended piston made of quartz glass to ensure efficient light transmission. In addition, a 45°reflector was installed in the base to facilitate the capture of the flame signal. Figure 2 shows the original signal captured by the camera and Matlab post-processing (including cropping and coloring) after calculation. The original image was cropped to show only the window portion due to reflections around the original image window.
Figure 2. Comparison of images before and after processing.
To establish the relationship between the captured image and the soot temperature, the high-speed camera was calibrated in the blackbody furnace. This calibration established the relationship between the image and the calibration temperature under different filters, with the 550 nm band set as the green (G) base color and the 660 nm band as the red (R) base color. Figure 3 shows the setup of the blackbody furnace equipment along with the calibration diagram for the blackbody furnace. The gray scale value of the calibration image was used to fit the brightness temperature curve corresponding to the temperature of the blackbody furnace. Error analysis was carried out between the real temperature of each calibration image and the temperature obtained by the algorithm. It can be seen from Table 2 that within a certain temperature range, the absolute error between the real temperature and the solution temperature is less than 1%.
Figure 3. Black-body furnace and calibrating images.
Table 2. Error analysis of true temperature and solution temperature.
2.2. Two-Color Method
In this experiment, the two-color method based on thermal radiation theory was used to calculate the temperature field and KL factor. In this research, monochromatic images of R and G primary colors were obtained from signals captured by two high-speed cameras, and combined with the two-color method to analyze and process the distribution of soot temperature and KL factor. The methodology is briefly described in the following paragraph, and for more detailed information, please refer to the study by Zhao et al. [28].
The theory of radiation from solids shows that any object produces thermal radiation to the outside world. For a blackbody, the intensity of its monochromatic hemispherical radiation, according to Planck’s law, is obtained as
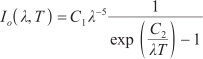
where is the intensity of the monochromatic hemispherical radiation of the flame;
and
are Planck’s first and second constants, with values of
,
, respectively;
is the wavelength of the radiation, and T is the blackbody temperature.
The actual object is not a blackbody, so the monochromatic hemispherical radiant intensity of the actual object is then the blackbody monochromatic hemispherical radiant intensity multiplied by a factor of
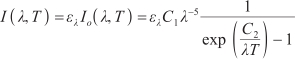
where is the monochromatic radiation coefficient, generally related to the temperature and wavelength, when its wavelength and solid temperature product is less than a certain value (), it can be simplified to the Wien formula as

At the same time, is alternatively defined as the brightness temperature of the actual object corresponding to the blackbody radiation intensity
as

In order to calculate the accuracy of the results, the two wavelengths selected should not be too close to each other, then it is necessary to introduce the Hottel-Broughton grayscale model [29], according to the grayscale model as
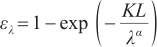
where K is the absorption coefficient, the value of which is approximately proportional to the number density of soot; L is the geometric thickness of the light path in the direction of detection; for general diesel engines, the coefficient is generally taken as 1.38 in the visible range.
For engineering purposes two different wavelengths(,
)under the KL is equal, and numerically can be done after the equation is removed to get two wavelengths corresponding to the brightness of the temperature
and
the relationship between the [28], for the

According to the fitting curve of the blackbody furnace calibration results, the actual temperature T is obtained by solving Equation (6) in combination with Newton’s iterative method.
An expression for the KL factor can also be obtained as

The actual temperature T obtained in Equation (1) is brought into Equation (7) to obtain the value of the corresponding KL factor.
2.3. Fuel Properties and Operation Conditions
This study examines the effect of blending PODE with diesel on the combustion and soot production of gasoline. The direct injection fuels used in the study are P0D100 (diesel), P20D80 (80% vol diesel, 20% vol PODE), P50D50 (50% vol diesel, 50% vol PODE), and P100D0 (PODE), with gasoline used as the low activity fuel. Table 3 presents the main physicochemical properties of the test fuels, where the physicochemical property parameters of 92# gasoline, 0# diesel, and PODE are obtained from experiments, and the fuel blends are derived from empirical formulas.
Table 3. Main properties of test fuels.
Throughout the entire testing process, the optical engine was naturally aspirated, and the speed was fixed at 1200 rpm. In order to stabilize combustion, the cooling water and intake temperature were controlled at 358 K and 363 K, respectively. After top dead center (ATDC), gasoline was injected into the intake manifold at -300°CA timing, pressurized to 0.5 MPa using compressed nitrogen gas (N2). PODE were delivered through a Bosch high-pressure common rail system, with the pressure maintained at 80 MPa. The total output energy was kept at 1400 J. The calculation process for the pre-mixed energy ratio is described by Equation (8).

In the equation, PER represents the premixed energy ratio, while and
denote the mass and low heating value (LHV) of the low-reactivity fuel. Similarly,
and
represent the mass and LHV of the PODE.
Table 4 and Table 5 give the test conditions for single injection and two-end injection respectively.
Table 4. Test conditions for a single injection strategy.
Table 5. Test conditions for two-stage injection strategy.
3. Results and Discussion
3.1. Effect of Single Injection Strategy on Combustion and Soot Formation Characteristics
3.1.1. Effects of High and Low Active Fuel Proportion and Blending Ratio on Combustion Characteristics
Figure 4 shows the curves of peak in-cylinder pressure variation for four different fuels at injection moments of -25°CA·ATDC with varying premixing ratios. It is observed that increasing the gasoline premix ratio results in a decrease in peak pressure for all four fuel types, and this trend is consistent. At 80% and 90% pre-mixing ratios, four fuels exhibit lower peak pressures, indicating suboptimal combustion performance. This phenomenon can be attributed to the better vaporization latent heat of the pre-mixed gas, which reduces the thermal environment within the combustion chamber. Simultaneously, the reduced direct injection of fuel leads to a lower overall cetane number of the fuel inside the combustion chamber. As the gasoline premix ratio is reduced below 70%, there is a tendency for the peak in-cylinder pressure to increase linearly. The observed effects can be attributed to the increased amount of direct in-cylinder fuel injection and increased cetane number. As the PODE blend ratio increases, the peak pressure per cycle decreases at the same premix ratio. This is due to the fact that the low calorific value of PODE is only 23.1 MJ/kg, slightly lower than that of diesel. Consequently, PODE requires a greater injection pulse width to deliver the same energy, which means indicating a greater injection volume. Based on the better heat release performance under a 50% pre-mixing ratio, subsequent studies were conducted under this condition.
Figure 4. Peak combustion pressure of four fuels at different premix ratios.
Figure 5 shows the peak in-cylinder pressures of the four fuels at different injection timings when the premixing ratio is 50%. It can be observed that the peak pressure decreases as the PODE blend ratio increases. In addition, it was observed that the peak pressure increases as the injection timing is delayed, with a significant upward trend between -40°CA·ATDC(crank angle after top dead center) and -30°CA·ATDC. This phenomenon can be attributed to the shorter blending time of the premixed gas in the cylinder, resulting in more significant local concentration and active stratification in the cylinder and intensified combustion.
Figure 5. Peak combustion pressure of four fuels at different injection timing.
In order to further investigate the effect of injection timing on combustion characteristics, a direct injection fuel of P50D50 with a fixed premix ratio of 50% was selected. Figure 6a shows the curves of cylinder pressure, heat release rate and combustion phase under different injection timing. Using the heat release rate curve shown in Figure 6a, the combustion start point (CA10), the combustion center (CA50), and the end point (CA90) are determined as the specific times when 10%, 50%, and 90% of the total calorific value are released, respectively. These points serve as key markers for analysis of the combustion process. The ignition delay period is the time from fuel injection to CA10, while the combustion duration is the time from CA10 to CA90. It was found that the total pressure in the cylinder was low and the peak pressure was only 2.795 MPa when the injection timing was -40°CA·ATDC. As the injection timing was delayed, the heat release rate increased from 31.2 J/°C to 119.2 J/°C, and the peak pressure increased from 2.795 MPa to 4.482 MPa, which is consistent with the results of the peak cylinder pressure in Figure 5. When the injection timing is delayed to -20°CA·ATDC, the combustion phase is delayed by approximately 11.488°CA. Therefore, to ensure optimal thermal efficiency, choosing an injection timing of -25°CA·ATDC is recommended for achieving the best combustion performance.
Figure 6. (a) P50D50 cylinder pressure and heat release rate curves at different injection times and (b) Four kinds of fuel cylinder pressure and heat release rate curves.
Figure 6b shows cylinder pressure and heat release rate curves and combustion phase curves for four fuel premix ratios of 50% and -25°CA·ATDC injection times. It was observed that for direct injection fuels P0D100, P20D80, and P50D50, the peak heat release rate was essentially the same, and the total amount of heat released did not change significantly. Compared to direct injection P0D100, the peak pressure for direct injection P100D0 was reduced by 18.52%, and the peak heat release rate was reduced by 27.18%. The observations indicate that PODE shows promise in mitigating combustion detonation under high load conditions in RCCI combustion. Simultaneously, with an increase in the blending ratio of PODE, the ignition delay extends, and the combustion phase shifts from 8.638°CA to 11.352°CA. However, when the direct-injection fuel is P50D50, the combustion ignition delay is prolonged, and the combustion duration is shortened by 0.287°CA compared to diesel, leading to a more concentrated release of heat, which helps to improve engine efficiency [30]. In addition, it can be seen from Table 3 that the kinematic viscosity of P0D100 is 4.8 mm2/s, and its numerical value is high, so it is difficult to get the ideal crushing effect in the process of in-cylinder spray, so that the atomization is not sufficient and the mixture in the cylinder is not uniform, which leads to poor combustion effect. But the kinematic viscosity of P100D0 is only 1.05 mm2/s. Too low fuel viscosity will lead to poor lubrication performance and aggravate the wear of oil pump and other oil road parts. And under the same injection pressure, the lower kinematic viscosity will reduce the spray cone angle, increase the spray penetration, and aggravate the fuel wall collision phenomenon, which will affect the combustion effect. However, when diesel is mixed with 50%PODE, the kinematic viscosity of the mixed fuel decreases from 4.8 mm2/s to 2.93 mm2/s, which greatly improves the lubrication performance of diesel fuel [31].
3.1.2. Effect of PODE Blending Ratio on the Formation Characteristics of Soot
To further investigate the effect of the PODE blend ratio on the formation and development of soot, this section uses a high-speed camera combined with the two-color method to quantify the amount of soot produced in the cylinder. Since PODE has reduced combustion efficiency, the images collected after filtering did not show obvious soot. Therefore, this section selected direct injection fuel for P0D100, P20D80, and P50D50 with a fixed gasoline premix ratio of 50%, direct injection time at -25 °CA·ATDC, and pre-injection time at -300 °CA·ATDC.
This section describes Figure 7, which shows the soot temperature and KL factor plots for different crank angles of the three fuels. The central region of soot with higher light intensity and temperature corresponds to the higher KL factor, while the lower light intensity and temperature at the edge position corresponds to the low KL factor region. As the PODE blend ratio increases, the initial position of soot temperature and KL factor shifts slightly backward, and the high temperature region and high KL factor region subsequently decrease, which is consistent with the combustion characteristics in Figure 6b. As the crank angle changes, the temperature and KL factor areas shift clockwise along the circumference. This is due to the intake valve is located on the right side of the window, causing a clockwise vortex in the cylinder. The vortex disturbance results in a relatively large local equivalence ratio on the right side of the window, which, combined with the reduced oxygen content due to combustion, makes this region more conducive to concentrated soot formation. As the PODE blend ratio increases, the soot changes from agglomerates to dots due to the increased oxygen content in the cylinder, making the soot more susceptible to oxidation. Soot appears in the center of the late combustion window because the pressure drop in the injector cavity at the end of injection, causes poor fuel atomization and accumulation of soot. The area of soot in the center of the cluster decreases as the PODE blend ratio increases, which can be attributed to the lower viscosity of PODE compared to diesel [32], leading to a reduction in this phenomenon. This conclusion is consistent with the research of Pastor et al., as an increase in the PODE blending ratio leads to a decrease in soot formation [33].
Figure 7. Soot temperature and KL images of three fuels.
Figure 8 shows the soot temperature distribution and the KL factor distribution, which characterize the soot concentration for the three fuels. The inset of the figure shows the beginning and end of the soot period. It was observed that the total amount of soot, the peak value, and the high temperature region decreased as the PODE blend ratio increased. When the PODE blending ratio exceeded 50%, almost no soot was observed, this is consistent with the findings of Ma et al. [24]. The total soot, peak soot, and high temperature range produced by direct injection fuel P20D80 and P50D50 were 55.22% and 36.55%, 61.02% and 44.89%, and 47.02% and 26.68% of direct injection fuel P0D100, respectively. The results suggest that increasing the PODE blend ratio has a significant effect on the inhibition of soot. Firstly, increasing the PODE blend ratio increases the total oxygen content in the cylinder, which promotes the subsequent oxidation of soot. This can be attributed to aromatic hydrocarbons (PAH) are precursors of soot formation [34], while PODE’s molecular formula (CH3O-(CH2O)n-CH3) contains only C-O and C-H bonds, with no C-C bonds or aromatic hydrocarbons [35]. The reduction of C-C bonds in the cylinder slows the dehydrogenation of ethylene and acetylene, and accelerates the oxidation process of cyclic hydrocarbons, resulting in an overall reduction of soot [36].
Figure 8. Distribution of soot temperature and KL factor of three fuels.
Figure 9 displays the averaged temperatures and KL factors of points in the soot images after arithmetic averaging. It can be observed that within the range from 3°CA to 10°CA, both the temperature and KL factor show a fluctuating increase. This may be attributed to the two stages of heat release: the first stage combustion is caused by the compression ignition of direct-injected fuel, and the second stage heat release is due to the ignition of the cylinder pre-mixture by the combustion of the direct-injected fuel. From Figure 9a,b, it can be seen that with the increase in PODE blending ratio, the average temperature of stable soot generation decreases from 2196.69 K to 2190.04 K and 2175.79 K. The stable average KL factor values decrease by 10.35% and 16.12% compared to the value under P0D100. The analysis suggests that PODE has a lower calorific value than diesel, which lowers the temperature in the combustion chamber due to its higher latent heat of vaporization, thereby reducing the generation of soot in high-temperature regions. Additionally, the oxygen content of PODE helps alleviate local oxygen deficiency in the combustion chamber, promoting the oxidation of soot in the later stages.
Figure 9. The average soot temperature, KL factor of three fuels. (a) Mean temperature. (b) Mean KL factor.
3.2. Effects of Two Injection Strategies on Combustion and Soot Formation Characteristics
3.2.1. Effect of Pre-Main Injection Time and Proportion on Combustion Characteristics
In order to further optimize combustion for reduced soot emissions, we conducted further optimization of the injection strategy by exploring the effectiveness of staged injection. Figure 10 shows the comparison results of the cylinder pressure and heat release rate under two injection strategies with three pre-main injection ratios at different pre-main injection times and a single injection strategy. Taking the results of Figure 10a (10% pre-injection/90% main injection) as an example, the peak cylinder pressure and heat release rate under the single injection strategy are higher than all the two-injection strategies. The peak cylinder pressure is 4.49 MPa, and the peak heat release rate is 121.95 J/°C, with the highest rate of pressure rise. This conclusion is consistent with the findings of Choi et al.’s research [37]. For the staged injection strategy, with the advance of pre-injection timing, both peak cylinder pressure and heat release rate increase, but they are both lower than those of the single injection [38]. The total heat release of the D-40/-20 condition is 94.26% of that of the single injection strategy, indicating better combustion performance. However, as the pre-injection timing is delayed, both the peak cylinder pressure and the heat release rate decrease, and the rate of pressure rise continuously decreases [39]. The analysis suggests that advancing the pre-injection timing results in a more uniform mixture of the pre-mixed gas in the cylinder. This is conducive to pre-mixed combustion, leading to a phenomenon of multi-point autoignition in combustion. As a result, there is an upward trend in cylinder pressure and heat release rate. Meanwhile, the comparative results in Figure 10b,c indicate that the peak cylinder pressure and heat release rate under the dual-injection strategy are both lower than those under single injection. When the pre-main injection ratio is 20%/80%, the peak cylinder pressure is 4.18 MPa and the peak heat release rate is 84.09 J/°CA. Moreover, this trend becomes more pronounced with an increase in the pre-injection ratio. Therefore, under the staged injection strategy, adopting a pre-injection ratio of 10% and main injection ratio of 90% leads to favorable cylinder pressure and heat release characteristics. In addition, the delay of the pre-injection time leads to a decrease in the interval between the two injections, and the pre-injection fuel has not completely evaporated in the development process of entering the cylinder, the main injection fuel has already begun to be injected, and the resistance to the forward development of the main injection fuel has increased. as a result, the spray penetration decreases, the atomization effect becomes worse, and the combustion effect deteriorates [40]. The analysis shows that when the pre-injection ratio increases and the main injection ratio decreases, the amount of main injection which plays the role of ignition decreases, so that the change of the pre-main injection time has little effect on the in-cylinder pressure and heat release rate. From another point of view, it is considered that the pulse width of the pre-injection increases, the pulse width of the main injection decreases, the interval between the two injections decreases, and the disturbance caused by the pre-injection into the cylinder increases, which leads to the increase of the resistance of the main injection into the cylinder. as a result, the spray penetration of the main injection fuel decreases, the atomization effect becomes worse, and the combustion effect worsens [40].
Figure 10. Cylinder pressure and heat release rate curves and combustion phase at different pre injection and main injection timings. (a) 10% pre injection/90% main injection. (b) 20% pre injection/80% main injection. (c) 30% pre injection/70% main injection.
3.2.2. Influence of Pre-Main Injection Time on Soot Generation Characteristics
Furthermore, employing a two-color method under the condition of 10% pre-injection and 90% main injection, with a main injection timing of -20°CA ATDC and pre-injection timings of (-40, -35, -30°CA ATDC), we investigate the influence of pre-main injection timing on soot formation.
Figure 11 illustrates the temperature field and corresponding KL factor under both segmented injection and single injection strategies. The total number of soot pixels in each image represents the overall amount of soot. It can be observed that the total soot amount is highest under the single injection strategy, with D-40/-20, D-35/-20, and D-30/-20 accounting for 35.12%, 10.99%, and 5.86% of S-20, respectively. Under the segmented injection strategy, soot generation is significantly reduced. This may be attributed to the small amount of pre-injection, which leads to a more uniform mixture of fuel and air in the combustion chamber, thereby reducing soot formation in high equivalence ratio regions. Simultaneously, due to the mixing of PODE, the spray quality of diesel and the effect of air mixing are improved [41]. The study by Herfatmanesh et al. [42]. suggests that staged injection has the potential to simultaneously reduce both NOX and soot emissions. However, in actuality, their research found that the two-stage strategy led to higher soot emissions. This was attributed to the timing of the second injection. In their experiment, the second injection occurred at the top dead center, resulting in a locally rich mixture and poor gas mixing. In contrast, in this study, the second injection timing was at -20°CA·ATDC, allowing more time for the main injection fuel to mix with the pre-mixed gas. As a result, higher soot emissions were not observed.
Figure 11. Soot temperature and KL images at different pre-injection and main-injection timings.
Figure 12 depicts the temperature and KL factor distributions of soot. It is observed that the segmented injection strategy has a significant effect on reducing soot. The instantaneous peak values of soot under D-40/-20, D-35/-20, and D-30/-20 are 29.66%, 20.17%, and 9.96% of that under S-20, respectively. Under the segmented injection strategy, with the delay of pre-injection time, the total amount of high-temperature regions continuously decreases. Specifically, D-40/-20, D-35/-20, and D-30/-20 account for 43.82%, 12.95%, and 5.74% of the total high-temperature regions under S-20. Furthermore, as the pre-injection time is delayed, the total amount of high KL factor regions (greater than 0.6) continues to decrease. Specifically, D-40/-20, D-35/-20, and D-30/-20 represent 30.37%, 4.88%, and 2.40% of the total KL factor regions under S-20.
Figure 12. Distribution of soot temperature and KL factor at different pre-injection and main-injection timings.
Figure 13 presents the averaged temperatures and KL factors of points in the soot images processed by the algorithm. As shown in Figure 13a, all four conditions undergo a fluctuation process characterized by an initial rise, followed by a decline, eventually stabilizing before disappearing. Under the single injection strategy, the average temperature of soot generation stabilizes at 2042.94 K. Meanwhile, under D-40/-20, D-35/-20, and D-30/-20, the average temperatures after stable soot generation are 2100.85 K, 2210.16 K, and 2192.24 K, respectively. In Figure 13b, it can be observed that the stable values of average KL factors decrease with the delay of pre-injection time. Specifically, under D-40/-20, D-35/-20, and D-30/-20, the stable average KL factors for soot are 86.52%, 66.62%, and 62.79% of those under S-20, respectively.
Figure 13. The average soot temperature, KL factor and synthetic KL gradient of three fuels. (a) Mean temperature. (b) Mean KL factor.
4. Conclusions
In this study, the combustion characteristics of diesel/gasoline dual-fuel RCCI combustion mode and the effects of PODE blend ratio and injection strategy on soot generation and evolution were investigated using high-speed imaging technology combined with two-color technology. Within the selected parameter range in this paper, the following conclusions were drawn from this experimental study.
(1) When the pre-mixture ratio is 50%, delaying the injection timing can increase the peak pressure and heat release rate while shortening the ignition time. With an injection timing of -20°CA·ATDC, the combustion phase is delayed. In comparison, -25°CA·ATDC proves to be the more favorable timing.
(2) When the premixing ratio is 50%, increasing the PODE blend ratio results in a decrease in the total heat release, soot, and soot peak of a single cycle. The total heat release, soot, and soot peak of single cycle combustion for direct injection P20D80 and P50D50 are 97.89% and 95.39% of the total heat release of direct injection P0D100, and 55.22% and 36.55% of the soot, and 61.02% and 44.89% of the soot peak, respectively. Therefore, P50D50 not only ensures good combustion characteristics, but also reduces soot formation and subsequent oxidation.
(3) As the PODE blend ratio increases, the soot formation changes from pellet shape to dot shape. In addition, as the crankshaft angle changes, the stable values of P20D80 and P50D50 decrease to 2190.04K and 2175.79K, respectively. In addition, the stable value of the KL factor decreases by 10.35% and 16.12%, respectively. It shows that the blending of PODE reduces the overall temperature in the cylinder, which promotes the low-temperature reaction and inhibits the generation of soot in the early stage, and at the same time plays a significant role in oxidizing soot in the later stage due to its own oxygen content.
(4) Under the staged injection strategy, the total amount of soot, the total amount in the high-temperature region, and the total amount in the high-KL factor region continue to decrease. Compared to S-20, the instantaneous peak values for D-40/-20, D-35/-20, and D-30/-20 are 29.66%, 20.17%, and 9.96%, respectively. The high-temperature region accounts for 43.82%, 12.95%, and 5.74%, respectively, compared to S-20. The high-KL factor region accounts for 30.37%, 4.88%, and 2.40%, respectively, compared to S-20. In summary, the staged injection strategy can effectively suppress the formation of soot, albeit at the expense of some thermal efficiency.
Author Contributions: Conceptualization, X.L. and P.J.; methodology, X.L.; software, B.G.; validation, B.G. and X.L; formal analysis, B.G.; investigation, B.G.; resources, X.L.; data curation, B.G. and X.L.; writing—original draft preparation, B.G.; writing—review and editing, B.G.; visualization, L.X.; supervision, P.J.; project administration, W.Z.; funding acquisition, W.Z and Q.W. All authors have read and agreed to the published version of the manuscript.
Funding: Funding for this research was provided by the National Natural Science Foundation of China (Nos.52076103).
Data Availability Statement: Not applicable.
Conflicts of Interest: The authors declare no conflict of interest.
References
- Sun, L.L.; Cui, H.J.; Ge, Q.S. Will China achieve its 2060 carbon neutral commitment from the provincial perspective? Advances in Climate Change Research 2022, 13(2), 169–178. DOI: https://doi.org/10.1016/j.accre.2022.02.002
- Dec, J.E. Advanced compression-ignition engines—Understanding the in-cylinder processes. Proceedings of the Combustion Institute 2009, 32(2), 2727–2742. DOI: https://doi.org/10.1016/j.proci.2008.08.008
- Wu, H.W.; Wang, R.H.; Ou, D.J.; et al. Reduction of smoke and nitrogen oxides of a partial HCCI engine using premixed gasoline and ethanol with air. Applied Energy 2011, 88(11), 3882–3890. DOI: https://doi.org/10.1016/j.apenergy.2011.03.027
- Singh, A.P.; Agarwal, A.K. Combustion characteristics of diesel HCCI engine: An experimental investigation using external mixture formation technique. Applied Energy 2012, 99, 116–125. DOI: https://doi.org/10.1016/j.apenergy.2012.03.060
- Saxena, S.; Bedoya, I.D. Fundamental phenomena affecting low temperature combustion and HCCI engines, high load limits and strategies for extending these limits. Progress in Energy and Combustion Science 2013, 39(5), 457–488. DOI: https://doi.org/10.1016/j.pecs.2013.05.002
- Komninos, N.P. Assessing the effect of mass transfer on the formation of HC and CO emissions in HCCI engines, using a multi-zone model. Energy Conversion and Management 2009, 50(5), 1192–1201. DOI: https://doi.org/10.1016/j.enconman.2009.01.026
- Das, P.; Subbarao, P.M.V.; Subrahmanyam, J.P. Effect of main injection timing for controlling the combustion phasing of a homogeneous charge compression ignition engine using a new dual injection strategy. Energy Conversion and Management 2015, 95, 248–258. DOI: https://doi.org/10.1016/j.enconman.2015.02.018
- Reitz, R.D.; Duraisamy, G. Review of high efficiency and clean reactivity controlled compression ignition (RCCI) combustion in internal combustion engines. Progress in Energy and Combustion Science 2015, 46, 12–71. DOI: https://doi.org/10.1016/j.pecs.2014.05.003
- Thongchai, S.; Lim, O. Investigation of the combustion characteristics of gasoline compression ignition engine fueled with gasoline-biodiesel blends. Journal of Mechanical Science and Technology 2018, 32(2), 959–967. DOI: https://doi.org/10.1007/s12206-018-0146-9
- Kokjohn, S.L.; Hanson, R.M.; Splitter, D.A.; et al. Fuel reactivity controlled compression ignition (RCCI): A pathway to controlled high-efficiency clean combustion. International Journal of Engine Research 2011, 12(3), 209–226. DOI: https://doi.org/10.1177/1468087411401548
- Wang, X.; Gao, J.; Chen, H.; et al. Diesel/methanol dual-fuel combustion: An assessment of soot nanostructure and oxidation reactivity. Fuel Processing Technology 2022, 237, 107464. DOI: https://doi.org/10.1016/j.fuproc.2022.107464
- Zheng, Z.; Xia, M.; Liu, H.; et al. Experimental study on combustion and emissions of n-butanol/biodiesel under both blended fuel mode and dual fuel RCCI mode. Fuel 2018, 226, 240–251. DOI: https://doi.org/10.1016/j.fuel.2018.03.151
- Jin, C.; Pang, X.; Zhang, X.; et al. Effects of C3–C5 alcohols on solubility of alcohols/diesel blends. Fuel 2019, 236, 65–74. DOI: https://doi.org/10.1016/j.fuel.2018.08.129
- Jin, C.; Geng, Z.; Liu, X.; et al. Effects of water content on the solubility between Isopropanol-Butanol-Ethanol (IBE) and diesel fuel under various ambient temperatures. Fuel 2021, 286, 119492. DOI: https://doi.org/10.1016/j.fuel.2020.119492
- Atmanli, A. Effects of a cetane improver on fuel properties and engine characteristics of a diesel engine fueled with the blends of diesel, hazelnut oil and higher carbon alcohol. Fuel 2016, 172, 209–217. DOI: https://doi.org/10.1016/j.fuel.2016.01.013
- Yilmaz, N.; Atmanli, A.; Hall, M. J.; et al. Determination of the Optimum Blend Ratio of Diesel, Waste Oil Derived Biodiesel and 1-Pentanol Using the Response Surface Method. Energies, Multidisciplinary Digital Publishing Institute 2022, 15(14), 5144. DOI: https://doi.org/10.3390/en15145144
- Liu, H.; Wang, Z.; Wang, J.; et al. Performance, combustion and emission characteristics of a diesel engine fueled with polyoxymethylene dimethyl ethers (PODE3-4)/ diesel blends. Energy 2015, 88, 793–800.
- Wang, Z.; Liu, H.; Ma, X.; et al. Homogeneous charge compression ignition (HCCI) combustion of polyoxymethylene dimethyl ethers (PODE). Fuel 2016, 183, 206–213. DOI: https://doi.org/10.1016/j.fuel.2016.06.033
- Iannuzzi, S.E.; Barro, C.; Boulouchos, K.; et al. POMDME-diesel blends: Evaluation of performance and exhaust emissions in a single cylinder heavy-duty diesel engine. Fuel 2017, 203, 57–67. DOI: https://doi.org/10.1016/j.fuel.2017.04.089
- Duraisamy, G.; Rangasamy, M.; Govindan, N. A comparative study on methanol/diesel and methanol/PODE dual fuel RCCI combustion in an automotive diesel engine. Renewable Energy 2020, 145, 542–556. DOI: https://doi.org/10.1016/j.renene.2019.06.044
- Tong, L.; Wang, H.; Zheng, Z.; et al. Experimental study of RCCI combustion and load extension in a compression ignition engine fueled with gasoline and PODE. Fuel 2016, 181, 878–886. DOI: https://doi.org/10.1016/j.fuel.2016.05.037
- Barro, C.; Parravicini, M.; Boulouchos, K.; et al. Neat polyoxymethylene dimethyl ether in a diesel engine; part 2: Exhaust emission analysis. Fuel 2018, 234, 1414–1421.
- Barro, C.; Parravicini, M.; Boulouchos, K.; et al. Neat polyoxymethylene dimethyl ether in a diesel engine; part 2: Exhaust emission analysis. Fuel 2018, 234, 1414–1421. DOI: https://doi.org/10.1016/j.fuel.2018.07.108
- Ma, Y.; Cui, L.; Ma, X.; et al. Optical study on spray combustion characteristics of PODE/diesel blends in different ambient conditions. Fuel 2020, 272, 117691. DOI: https://doi.org/10.1016/j.fuel.2020.117691
- Pellegrini, L.; Marchionna, M.; Patrini, R.; et al. Emission Performance of Neat and Blended Polyoxymethylene Dimethyl Ethers in an Old Light-Duty Diesel Car. SAE Technical Paper 2013, No. 2013- 01 –1035. DOI: https://doi.org/10.4271/2013-01-1035
- Shi, Y.; Lu, Y.; Cai, Y.; et al. Evolution of particulate matter deposited in the DPF channel during low-temperature regeneration by non-thermal plasma. Fuel 2022, 318, 123552. DOI: https://doi.org/10.1016/j.fuel.2022.123552
- Shi, Y.; Zhou, Y.; Li, Z.; et al. Effect of temperature control conditions on DPF regeneration by nonthermal plasma. Chemosphere 2022, 302, 134787. DOI: https://doi.org/10.1016/j.chemosphere.2022.134787
- Zhao, H.; Ladommatos, N. Optical diagnostics for soot and temperature measurement in diesel engines. Progress in Energy and Combustion Science 1998, 24(3), 221–255. DOI: https://doi.org/10.1016/S0360-1285(97)00033-6
- Hottel, H.C.; Broughton, F.P. Determination of True Temperature and Total Radiation from Luminous Gas Flames. Industrial & Engineering Chemistry Analytical Edition 1932, 4(2), 166–175. DOI: https://doi.org/10.1021/ac50078a004
- Liu, H.; Wang, Z.; Wang, J.; et al. Performance, combustion and emission characteristics of a diesel engine fueled with polyoxymethylene dimethyl ethers (PODE3-4)/ diesel blends. Energy 2015, 88, 793–800. DOI: https://doi.org/10.1016/j.energy.2015.05.088
- Huilgol, R.R.; You, Z. On the importance of the pressure dependence of viscosity in steady non-isothermal shearing flows of compressible and incompressible fluids and in the isothermal fountain flow. Journal of Non-Newtonian Fluid Mechanics 2006, 136(2), 106–117. DOI: https://doi.org/10.1016/j.jnnfm.2006.03.011
- Liu, J.; Sun, P.; Huang, H.; et al. Experimental investigation on performance, combustion and emission characteristics of a common-rail diesel engine fueled with polyoxymethylene dimethyl ethers-diesel blends. Applied Energy 2017, 202, 527–536. DOI: https://doi.org/10.1016/j.apenergy.2017.05.166
- Pastor, J.V.; García, A.; Micó, C.; et al. Simultaneous high-speed spectroscopy and 2-color pyrometry analysis in an optical compression ignition engine fueled with OMEX-diesel blends. Combustion and Flame 2021, 230, 111437. DOI: https://doi.org/10.1016/j.combustflame.2021.111437
- Liu, J.; Liu, Z.; Wang, L.; et al. Effects of PODE/diesel blends on particulate matter emission and particle oxidation characteristics of a common-rail diesel engine. Fuel Processing Technology 2021, 212, 106634. DOI: https://doi.org/10.1016/j.fuproc.2020.106634
- Liu, J.; Feng, L.; Wang, H.; et al. Spray characteristics of gasoline/PODE and diesel/PODE blends in a constant volume chamber. Applied Thermal Engineering 2019, 159, 113850. DOI: https://doi.org/10.1016/j.applthermaleng.2019.113850
- Ren, S.; Wang, Z.; Li, B.; et al. Development of a reduced polyoxymethylene dimethyl ethers (PODEn) mechanism for engine applications. Fuel 2019, 238, 208–224. DOI: https://doi.org/10.1016/j.fuel.2018.10.111
- Choi, M.; Park, S. Optimization of multiple-stage fuel injection and optical analysis of the combustion process in a heavy-duty diesel engine. Fuel Processing Technology 2022, 228, 107137. DOI: https://doi.org/10.1016/j.fuproc.2021.107137
- Tang, Q.; Liu, H.; Ran, X.; et al. Effects of direct-injection fuel types and proportion on late-injection reactivity controlled compression ignition. Combustion and Flame 2020, 211, 445–455. DOI: https://doi.org/10.1016/j.combustflame.2019.10.018
- Li, B.; Xiao, G.; Zhang, H.; et al. Experimental study of independent two-stage in-cylinder heat release using jet controlled compression ignition. Fuel 2021, 289, 119925. DOI: https://doi.org/10.1016/j.fuel.2020.119925
- Zheng, Z.; Chen, P.; Yao, M.; et al. Experimental study on the partially premixed combustion (PPC) fueled with n-butanol. Fuel 2019, 257, 116000. DOI: https://doi.org/10.1016/j.fuel.2019.116000
- Liu, Y.; Tian, J.; Li, F.; et al. Spray characteristics of biodiesel-polyoxymethylene dimethyl ethers (PODE) blends in a constant volume chamber. Combustion Science and Technology 2023, 195(16), 4069–4091. DOI: https://doi.org/10.1080/00102202.2022.2056413
- Herfatmanesh, M.R.; Lu, P.; Attar, M.A.; et al. Experimental investigation into the effects of two-stage injection on fuel injection quantity, combustion and emissions in a high-speed optical common rail diesel engine. Fuel 2013, 109, 137–147. DOI: https://doi.org/10.1016/j.fuel.2013.01.013